Des rails bas carbone fabriqués en France
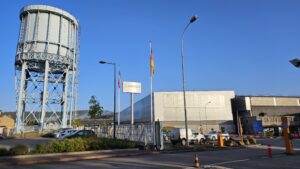
L’entrée du site industriel Saarstahl de Hayange
ISSU DU MAG DE MAI 2024 _ Auteur Fred PORCEL
Le 4 octobre 2023, nous avons eu la chance de visiter l’impressionnant site industriel de la société Saarstahl à Hayange, en région Lorraine. Savez-vous ce que cette usine fabrique ? Des rails pour chemins de fer ! En route pour une visite guidée…
Hayange, Moselle, 16 000 habitants
Ce site lorrain a 132 ans ! Inauguré en 1892, alors propriété de la famille Wendel, c’est un complexe industriel initialement destiné à fabriquer des poutrelles métalliques. Il s’oriente ensuite vers les rails, qu’il produit toujours aujourd’hui pour différents secteurs : lignes à grande vitesse, transports urbains, voies lourdement chargées, transports mixtes, ainsi que des rails pour appareils de voie.
L’usine emploie 450 personnes, elle est la seule en France à produire des rails. Il y en a d’autres en Europe : Italie, Espagne, Autriche, Tchéquie, Pologne, Luxembourg. Le site d’Hayange s’étend sur 14 hectares, dont une partie est couverte de voies ferrées pour convoyer les blooms qui arrivent et les rails qui repartent. Un bloom ? C’est une barre d’acier de section carrée et de longueur variable, destinée à être laminée pour obtenir des produits longs de section importante comme… des rails. L’usine de Saarstahl reçoit en moyenne un train de blooms par jour, produits presque exclusivement par Ascoval, une autre usine du groupe basée à Valenciennes. Grâce à ces blooms, le site d’Hayange fabrique 300 000 tonnes de rails par an, soit environ 100 km de rails par semaine, d’une centaine de types différents (selon la masse au mètre linéaire, la longueur, le profil), dont dix pour SNCF.
La société Saarstahl
Le site lorrain a connu de nombreux propriétaires aux profils très différents, parmi lesquels Sacilor, Usinor, l’indien Tata, British Steel… avant d’être racheté en 2021 par l’allemand Saarstahl, une fondation industrielle qui ne distribue pas de dividendes : les bénéfices sont réinvestis ou distribués aux salariés. Malgré ces rachats successifs, les effectifs n’ont pas baissé et la production n’a jamais cessé. Les clients, dont la SNCF, ont toujours soutenu l’activité et rempli les carnets de commandes. Avec un tel passé, quel avenir ? Saarstahl considère que l’acier a de l’avenir dans le transport par rail, alors qu’il est en perte de vitesse dans l’automobile en transition vers l’électrique, moins consommatrice d’acier. Notons que des rails fabriqués à Hayange ont été livrés dans l’est de l’Ukraine à l’été 2023, ils servent à reconstruire les infrastructures détruites depuis l’invasion russe.
La fabrication de l’acier
Pour produire l’acier nécessaire à la fabrication d’un rail, il y a plusieurs méthodes :
– la traditionnelle : dans un haut fourneau, on chauffe du minerai de fer avec du coke, une variété de charbon hautement calorifique, mais très polluante. Le minerai se transforme en fonte en fusion, dans laquelle on injecte de l’oxygène (c’est le bullage). L’oxygène se combine avec le carbone pour former du CO2, qui s’évacue par le gueulard, un orifice en haut du haut fourneau. L’acier liquide ainsi produit, débarrassé de son oxygène (on dit qu’il est réduit) et de son carbone (il en reste environ 0,8%) est ensuite coulé en continu et coupé pour former des blooms.
– la plus récente, utilisée par Ascoval, elle évite le bullage d’oxygène – et donc l’émission de CO2 – en utilisant, à la place du minerai de fer, différentes sortes de ferraille, auxquelles on ajoute des additifs pour correspondre à la composition de l’acier voulu, que l’on fait fondre grâce à de puissants arcs électriques.
– la prochaine, dite de réduction directe, consiste à chauffer le minerai en brûlant de l’hydrogène « vert ». En se combinant avec l’oxygène, il produit de la vapeur d’eau, sans émettre de CO2.
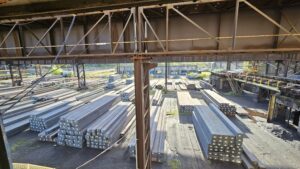
Différentes sortes de blooms, entreposés à l’extérieur des hangars
Du bloom au rail
L’acier fondu est coulé en continu pour produire des blooms qui seront ensuite laminés pour devenir des rails. Un bloom fait entre 5 et 6 tonnes, selon le type de rail attendu. Chaque bloom est identifié individuellement pour permettre une traçabilité durant toute la vie des rails qui seront fabriqués avec.
Les fours : à Hayange, ils fonctionnent tous les jours de l’année, peuvent accueillir chacun une quarantaine de blooms à la fois, qu’ils chauffent pendant 4 à 5 heures jusqu’à 1 300 degrés en brûlant du gaz fossile (qu’on appelait « naturel » au siècle passé). Au rythme d’environ 22 par heure, les blooms incandescents sont expulsés des fours et conduits par un système de rouleaux vers les ateliers de laminage, diffusant sur leur passage une infernale onde de chaleur !
Le laminage : les blooms rougeoyants glissent dans différentes cages successives équipées de cylindres de laminage (de plusieurs tonnes chacun), pour passer d’un profil cubique à celui du rail demandé par le client. Sur leur route où aucun humain n’est autorisé, de l’eau est projetée pour refroidir les rouleaux sur lesquels ils passent, générant des geysers de vapeur tout au long du parcours. Une fois laminé au profil voulu, le rail incandescent passe sous un nettoyeur à très haute pression qui va le débarrasser de ses déchets : la calamine, récupérée pour produire notamment de l’aluminium.
Le refroidissement : les rails laminés au profil voulu, encore très chauds, sont entreposés courbés, côte à côte, sur des rouleaux. Ils y passeront deux à trois heures, se redressant naturellement en refroidissant jusqu’à température ambiante.
La rectification : le rail refroidi, d’une longueur pouvant aller jusqu’à 108 mètres, glisse entre des rouleaux pour finir de se redresser parfaitement, avant de passer sous une roue qui martèle tous les trois mètres son numéro de série, unique, ainsi que son type.
Le contrôle : refroidi, redressé, marqué, surfant toujours sur un tapis de rouleaux, le rail entre dans l’atelier de contrôle. Il va y recevoir un code-barres et subir l’examen minutieux de roues calibrées, lasers, courants de Foucault et ultrasons pour vérifier qu’il respecte les valeurs strictes qui lui ont été imposées : longueur, cotes, profil, surface, fissures… S’il est validé, il part au hangar pour être stocké puis chargé sur des wagons, avant de partir pour le chantier qui l’attend et être mis en voie. Mais si une anomalie est relevée, une alarme retentit, une marque de peinture est apposée à l’endroit du défaut et le rail est conduit vers l’atelier de réparation.
La réparation : manipulé par un immense pont roulant à électro-aimants, chaque rail défectueux passe entre les mains d’une équipe de vérificateurs qui évaluent s’il est réparable ou pas. Selon le diagnostic, il sera rectifié, recoupé, voire, dans le pire des cas, renvoyé à l’usine Ascoval pour être refondu.
L’outillage : taillé à la hauteur des mastodontes d’acier incandescent qu’il reçoit, il dégrossit, lamine, martèle et profile 24/24. Une part importante de l’activité de l’usine consiste à entretenir et rectifier ces outillages massifs et ultra spécifiques, sans lesquels il serait impossible de produire.
Les ouvriers : ce site immense qui ne dort jamais semble quasiment désert, alors qu’il emploie près de 450 personnes. En fait, les ouvriers interviennent surtout lorsqu’un incident interrompt la chaîne de fabrication, ainsi que pour changer les outillages dans les laminoirs quand un nouveau type de rail entre en production. Ici et là, quelques petits groupes sont chargés d’évaluer et rectifier les défauts, contrôler la qualité, charger ou décharger les wagons, superviser les machines et le process de fabrication.
Le CO2 : l’ennemi du climat
La fabrication de l’acier a émis 2,6 milliards de tonnes de CO2 en 2021, soit 7% des émissions mondiales. Dans le processus de fabrication traditionnelle de l’acier, c’est l’utilisation de coke et le bullage de l’oxygène qui émettent le plus de CO2. En supprimant cette étape, la méthode par arcs électriques utilisée par Ascoval en émet trois fois moins. C’est la spécificité de la société Saarstahl : quand une tonne de rail fabriqué par processus traditionnel rejette dans l’atmosphère 2,8 tonnes de CO2, celui fabriqué par Saarstahl n’en rejette « que » 780 kg.
Économiquement, le coût global est proche de celui de la méthode traditionnelle, mais la composition de ce coût est différente. Une variable qui devrait prendre de l’importance est la valeur de la taxe carbone. Imposée par l’Europe, mais seulement à petits pas sous la pression des industriels obtenant exonérations et quotas gratuits, elle s’impose et se renchérit peu à peu, obligeant les aciéries classiques à se remettre en question. SNCF est partie prenante dans ce processus d’évolution « écologique », en revendant de vieux rails à Ascoval que celle-ci refond pour produire un nouvel acier, qu’elle coule sous forme de blooms expédiés à Hayange, qui les lamine pour fabriquer des rails neufs.
Le Mag tient à remercier très « chaleureusement » François Cristofari, directeur technique du site d’Hayange, qui a pris de son temps précieux pour nous accueillir et nous guider tout au long de cette visite inoubliable, ainsi que l’Union régionale de Lorraine (Jean-François Neisse et Benoît Thévenard) pour l’accompagnement et l’organisation de cette visite.